Advantages of Hydraulic Clamping
Hydraulic clamping systems are a powerful addition to any manufacturing process. They combine both the benefits of high-precision clamping with the power of automation. They offer their operators many benefits, which we will discuss in this engineering resource.
Learn more about the advantages of hydraulic clamps from Carr Lane Mfg.
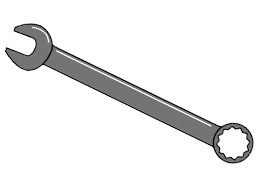
What Are Hydraulic Clamps Used For?
Hydraulic clamps are used in many machining processes, offering support for many production lines. Manual clamps are used to support a workpiece that is being cut or reshaped. Hydraulic clamps provide the same service as manual clamps, but they are much easier to operate and increase your production efficiency.
Hydraulic clamps can be used in any workholding application. They provide a similar function as manual clamps with several advantages.
First, hydraulic clamping reduces operator workload and load/unload times by automating the clamp/unclamp cycle. Second, since the clamping is automated clamping forces are more consistent part-to-part reducing workpiece non-conformities. Thirdly, hydraulic clamps allow for the automation of part loading/unloading.
How Do Hydraulic Clamps Work?
Hydraulic fluid is pressurized by a pump which results in force being applied to a piston in the clamp. The pressure advances the piston applying force to the workpiece. Single-acting clamps use hydraulic pressure to apply force to the workpiece and a spring to unclamp. Double-acting clamps use hydraulic pressure to both clamp and unclamp cycles.
Why Hydraulic Clamps Were Manufactured
Demand for faster production and more machine automation created the advanced power workholding systems we know today.
Advantages of Hydraulic Power Workholding
Hydraulic power workholding combines the benefits of high-precision clamping with the power of automation. They offer many advantages, including increased production rates, improved part quality, and automation. Continue reading to learn more.
Increase Your Production Rates
Faster Clamping
Increased clamping speed is one of the more obvious advantages of power workholding. A machine operator can activate the complete clamping system from a single point in a matter of seconds, decreasing the amount of time it takes to tighten and loosen the clamps.
The increased clamping speed thereby reduces the non-productive time which characterizes the loading and unloading cycles. But reduced loading time is only one reason to select power workholding.
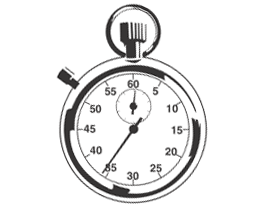
Faster Machining
In addition to the reduction of clamping time, power-workholding systems allow much faster machining cycles. Power clamps offer added security. Instead of relying on the operator to properly tighten the clamps, power-operated clamping systems provide consistent clamping forces.
Holding forces can also be adjusted to suit the specific requirements of the workpiece. This permits clamping forces to be increased, allowing heavier feeds and faster speeds.

How Hydraulic Clamps Improve Part Quality
Improved part quality is perhaps the greatest benefit of power-workholding systems. These systems improve the overall quality and reduce rejected or scrapped parts by providing consistent, controllable clamping forces and self-adjusting work supports.
- Consistent and repeatable operation
- Controlled clamping force
- Automatically adjusting work supports
Consistent and Repeatable Operation
A major feature of power-workholding systems is consistent and repeatable clamping forces. Manually operated clamps rely solely on the strength and diligence of the operator. Power clamps, however, are controlled by a power source, so the strength and fatigue level of the operator does not affect the clamping force.
Control of clamping force increases both the safety and efficiency of the machining operation. Likewise, with swing clamps, extending clamps, or other forms of self-positioning clamps, the position of the clamp on the workpiece is established by the clamp. Once properly set and positioned, power clamps perform the same way, part after part, throughout the production run. The amount of operator interaction is reduced, while consistency and repeatability are enhanced.
Controlled Clamping Force
Power-workholding systems are adjustable to provide exactly the right amount of clamping force. When either light or heavy clamping forces are required for a workpiece, the clamping force can be adjusted for those specific conditions.
A controlled clamping force is important for parts with varying thicknesses, brittle materials, odd shapes, or similar characteristics. Reduced clamping forces can be applied if the workpiece is delicate or has thin cross-sections, as with some cast parts. Conversely, if the workpiece requires greater holding forces, power clamps can also be adjusted for additional pressure.
Automatically Adjusting Work Supports
Many workpieces require additional support to prevent deflection or vibration during the machining cycle. In these cases, self-adjusting work supports are quite useful. These supports are placed under the workpiece and either advance to meet the workpiece or are depressed by loading the part in the fixture.
Once the required height is achieved, work supports are locked in position by hydraulic pressure and act as additional fixed locators throughout the machining cycle. At the time of unloading, the work supports return to the free position and are repositioned with the loading and clamping of a new part. So, virtually any differences in the supporting surface, such as steps or irregular features, are easily accommodated.
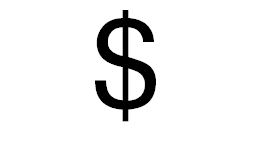
Automation Through Hydraulic Clamping
Automatic Sequencing
Automatic sequencing is the ability of a power-workholding system to operate clamps and other devices in a specific order. In many clamping situations, this feature is important. Power-workholding systems handle sequencing with one or more sequence valves in the hydraulic circuit. These valves activate the clamps and other devices at the proper time.
To reduce the chance of deformed parts, it may be necessary to activate clamps in a specific order. Self-adjusting work supports often reduce the chance of part deflection. When supports are used, the first operation in the sequence locks the supports under the part. Once the supports are in a fixed position against the workpiece, the clamps are brought into contact with the part.
The sequence of operation is also important when a clamp must be moved out of the way during a machining operation. A clamping valve moves the clamp out of the way as the cutter passes. When the cutter is clear, the valve then re-clamps the part. In almost every case, a power sequencing arrangement is much faster and more reliable than its manual counterpart.
Remote Clamp Operation
Most fixturing operations require more than one clamp to hold the workpiece. Of these clamps, some may be hard to reach, and present a safety hazard to the operator. A large workpiece, for example, may require six or more clamps to completely hold the part. Power clamps are typically operated together, from a single point.
Eliminate the hazard of machine operators reaching over the part to tighten a clamp close to a cutter by simply positioning the clamping valve away from the cutters. This single remote operating point greatly reduces the time and expense of manually positioning and tightening each clamp, while enhancing operator safety and eliminating hard-to-reach clamps.
Other Advantages of Hydraulic Clamping
Power-workholding systems offer several other advantages over manual clamping. These advantages include remote clamp operation, reduced operator fatigue, automatic sequencing, fixture compactness, and increased machine-tool capacity. These advantages are:
- Reduced operator fatigue
- Fixture compactness
- Increased machine-tool capacity
Reduced Operator Fatigue
Operator fatigue is a design consideration often overlooked. Most operators over-tighten clamps in the morning and under-tighten clamps in the afternoon. Power clamping systems reduce operator fatigue by replacing the strenuous activity of clamping manually with the consistent and controllable functioning of hydraulically actuated clamps. This consistency and control results in higher production rates.
Fixture Compactness
The compactness of the hydraulic clamp fixtures allows you to load more workpieces onto a fixture, which is caused by the clamps ability to be positioned closer together. One result of this change is increased productivity when the chip-cutting time is lengthened, and the percentage of time operator attention is required decreases.
Increased Machine-Tool Capacity
The consistent holding force of power clamps allows for faster machining rates. The increased production rates translate into greater capacity, especially important for expensive machine tools.