Steel Materials & Products Technical Information
Welcome to our comprehensive guide on the steel materials used in manufacturing and engineering applications. These are also the steel types we use in our products. We want to show you the different steel types and properties, helping you understand their uses and advantages.
Different Types of Steel
12L14 Steel
See 1215 steel below.
1215 Steel
1215 steel is a free-machining steel often considered alongside 12L14 steel. While both steels possess good machinability, 12L14, with its lead addition, has slightly superior machinability.
This case-hardening steel is ideal for many round and hex-shaped parts, offering strength, inherent flexibility, toughness, and fine surface finishes. Especially for threaded parts, this steel's free-machining qualities yield smooth machined surfaces and tight tolerances.
1215 steel also boasts superior case-hardening qualities. Most of our finished 1215 steel parts are carburize-hardened to provide a wear-resistant surface while retaining a rigid, ductile core. According to the AISI/SAE numbering system, the "12" signifies the steel's type (free-machining steel with added sulfur and phosphorus), while the "15" represents the carbon content in hundredths of a percent (0.15%).
1215 Steel Applications
- Machined Parts: Suitable for various precision components like bolts, screws, nuts, studs, and fittings.
- Bushings and Bearings: Utilized for bushings and bearings in machinery and equipment.
- Couplings: Utilized in making couplings for transmitting torque between shafts in mechanical systems.
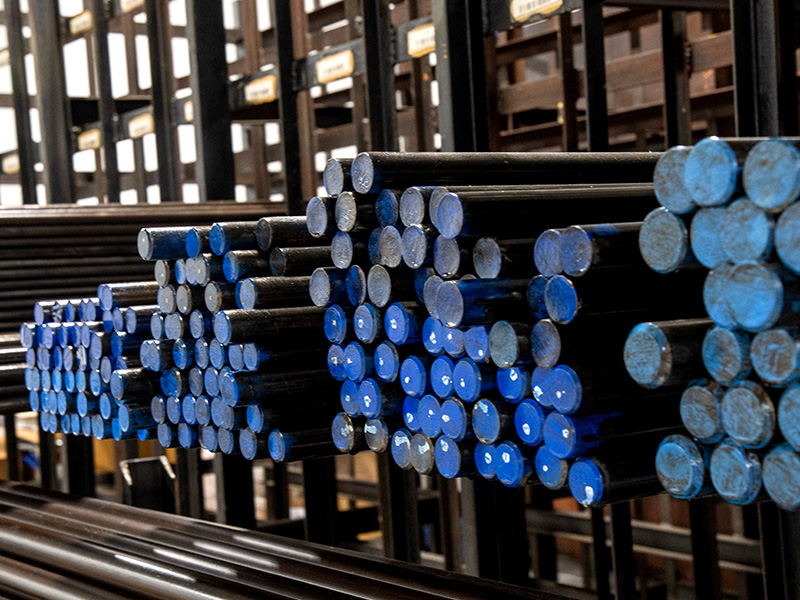
1018 Steel
1018 steel is our material of choice for rectangular parts. This low-carbon, case-hardening steel offers high strength, inherent flexibility, toughness, good surface finishes, and weldability. It also has excellent case-hardening qualities. We carburize-harden most of our finished 1018 parts to provide a wear-resistant surface while retaining a ductile core. According to the AISI/SAE numbering system, the "10" signifies the steel's type (plain carbon), and the "18" represents its carbon content in hundredths of a percent (0.18%).
1018 Steel Applications
- Structural Components: 1018 Steel is commonly used to construct structural components like I-beams, angles, channels, and flat bars.
- Construction Hardware: Used in the construction industry for producing hardware items like brackets, braces, and supports.
1144 Steel
1144 is a high-carbon, through-hardening steel ideal when high tensile and yield strength are needed. We use the "Stressproof" grade, which provides strength, elasticity, and minimal distortion after machining due to its manufacturing method and stress-relief heat treatment. According to the AISI/SAE numbering system, the "11" in 1144 indicates its type (free-machining steel with added sulfur), while the "44" signifies a carbon content of 0.44%.
1144 Steel Applications
- Shafts and Axles: Due to its high strength and fatigue resistance, this steel is often used to manufacture shafts and axles in machinery, automotive, and construction applications.
- Bushings and Couplings: Used to produce bushings and couplings that require high strength and resistance to wear and fatigue.
4130 Steel (Chromoly)
4130, an alloy steel, is often referred to as "Chromoly" due to its Chromium and Molybdenum content. This medium-carbon, through-hardening steel provides excellent tensile and yield strength, with a high resistance to cracking thanks to its flexibility and toughness. Carr Lane Mfg. prefers 4130 for applications under significant stress, especially where deformation is preferable over cracking. Almost every application of this material involves through-hardening. According to the AISI/SAE number system, the "41" in 4130 denotes its type (Chromium-Molybdenum Alloy), while the "30" reflects a carbon content of 0.30%.
4130 Steel Applications
- Aircraft and Aerospace: Ideal for gears, fittings, landing gear, brackets, and structural parts due to its strength-to-weight ratio.
- Automotive: Axles, connecting rods, crankshafts, and suspension components.
- Machinery: Gears, shafts, and other machine parts.
A-2 Steel
A-2 is a type of cold work tool steel with a very high carbon content (1.0%). The primary alloying elements are Chromium and Molybdenum. The "A" denotes that it's an air-hardening tool steel, contrasting with oil-hardening types requiring oil quenching. This material excels in applications valuing hardness, wear resistance, and toughness.
A-2 Steel Applications
- Cutting Tools: Suitable for knives, blades, punches, and shear blades.
- Metalworking Machinery: Parts subject to wear, impact, or abrasion.
A36 Steel
AASTM grade A36 is a hot-rolled, low-carbon steel known for its ductility, toughness, and weldability. It is generally used without heat treatment for thick plates or steel shapes such as I-Beams, angles, and channels.
A36 Steel Applications
- Structures: Widely used in construction for beams, columns, girders, and more.
- General Uses: For general fabrication, including welding, cutting, bending, and forming.
Invar 36 Steel
First invented in 1896 by a Swiss Physicist, this nickel-iron alloy has an extremely low Coefficient of Thermal Expansion (CTE) – so low that the inventor won the Noble Prize in 1920. Steel
It contains 36% Nickel, which is softer than steel and difficult to machine. Still, it is beneficial in applications where the product will undergo multiple heat-cool cycles and requires dimensional consistency. This material is not hardenable but is annealed for stress relief after machining. It is capable of being coated by hard materials, such as PVD.
Contact Us
Carr Lane Mfg. is a leading global manufacturer of steel tooling components. Please get in touch with our team for more details about different steel materials and how they can apply to your needs.
Contact Us