Inverted Bolt Systems
Several manufactures sell a Mechanical Quick-Change system that uses an inverted threaded fastener to provide locating and retention. These systems have excellent retention force but due to the nature of threads the location accuracy of these systems is often +/- 0.01”.
A threaded hole must be placed first in your fixture or workpiece. Then the workpiece is loaded onto a special subplate which contains the Inverted Bolt Fasteners. Once the workpiece has been aligned the fasteners can be threaded up and into the fixture of workpiece. Care must be taken to not damage the threads in a fixture over repeated uses. A Threaded insert can be used to provide a hard, steel, thread in an aluminum fixture plate.
These systems also require highly specialized sub-plates that can be cost-intensive to implement. As the Inverted Bolt Fasteners themselves can be expensive, they are frequently designed to be modular; such that they can be removed and inserted into different locations on the sub-plate.
Some manufacturers suggest Air Powered Impact guns be used to fasten these systems; a device that may apply too much force if the operator uses the gun on other workholding.
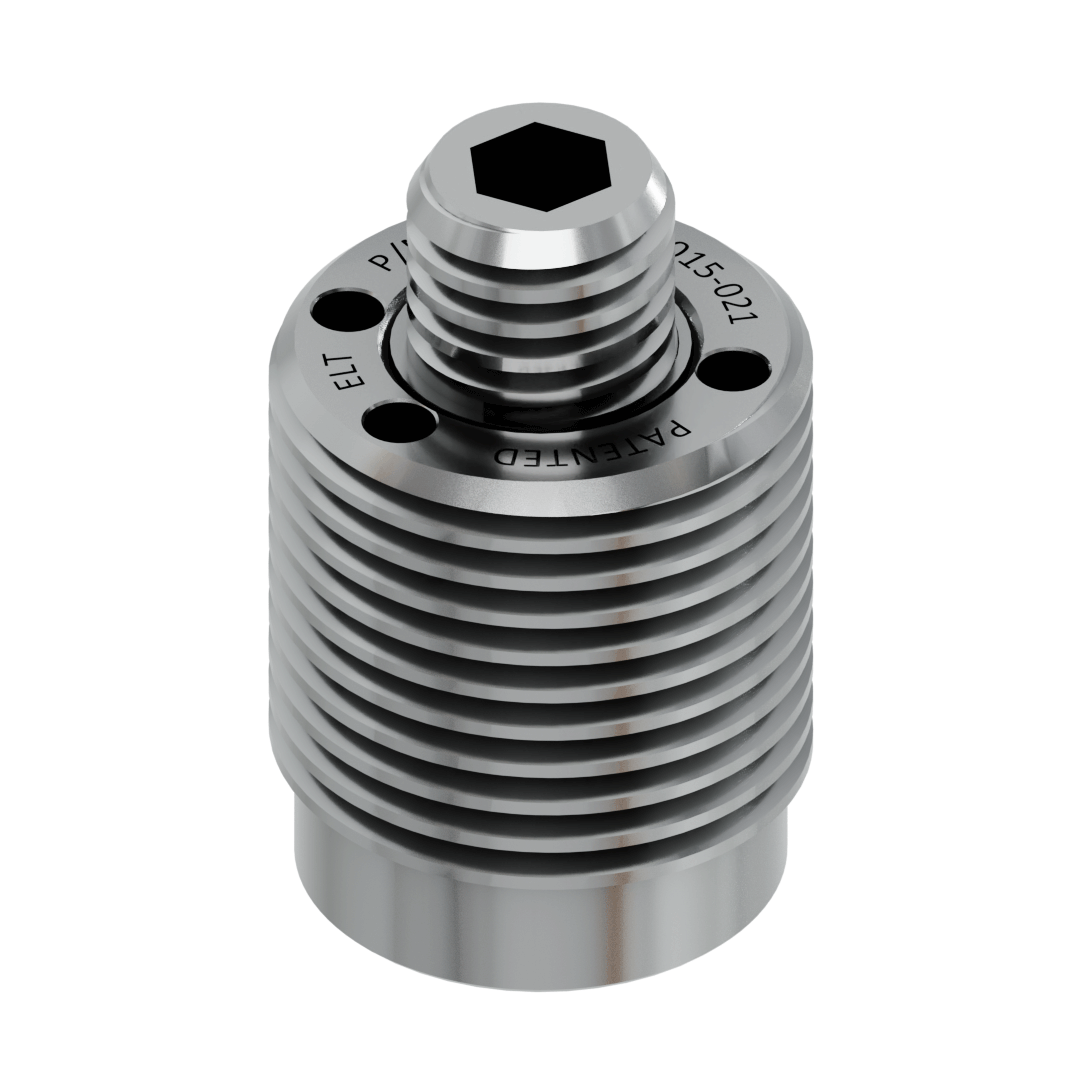
The most significant strength of these systems is the ability to bolt the workpiece directly to the machine; eliminating the need for other workholding. This does require a first operation to tap a hole in the workpiece and therefore has similar function to the Headless Carr Lock, and all Zero-Point systems with lower repeatability.
Fastener Quick Change Solutions
There are similar classic Fastener based solutions. These solutions are frequently more cost-effective and scalable as they can easily be integrated into commonly available threaded-bushed subplates. There are two main types of these systems: C-Washers and Quarter or Half-Turn Screws.
A C-Washer uses a hole in the fixture plate that is larger than the nut, or head, on a bolt that has been pre-inserted into the sub-plate. Once the fixture has been loaded, over the bolt, the C-Washer is inserted between the head of the bolt and the top of the fixture. Then a few turns of the wrench only are required to tighten the bolt. Location must be performed by other locating devices such as Locating Pins. The advantage of this system, over simply bolting the fixture to the sub-plate is the amount of wrenching required is greatly reduced.
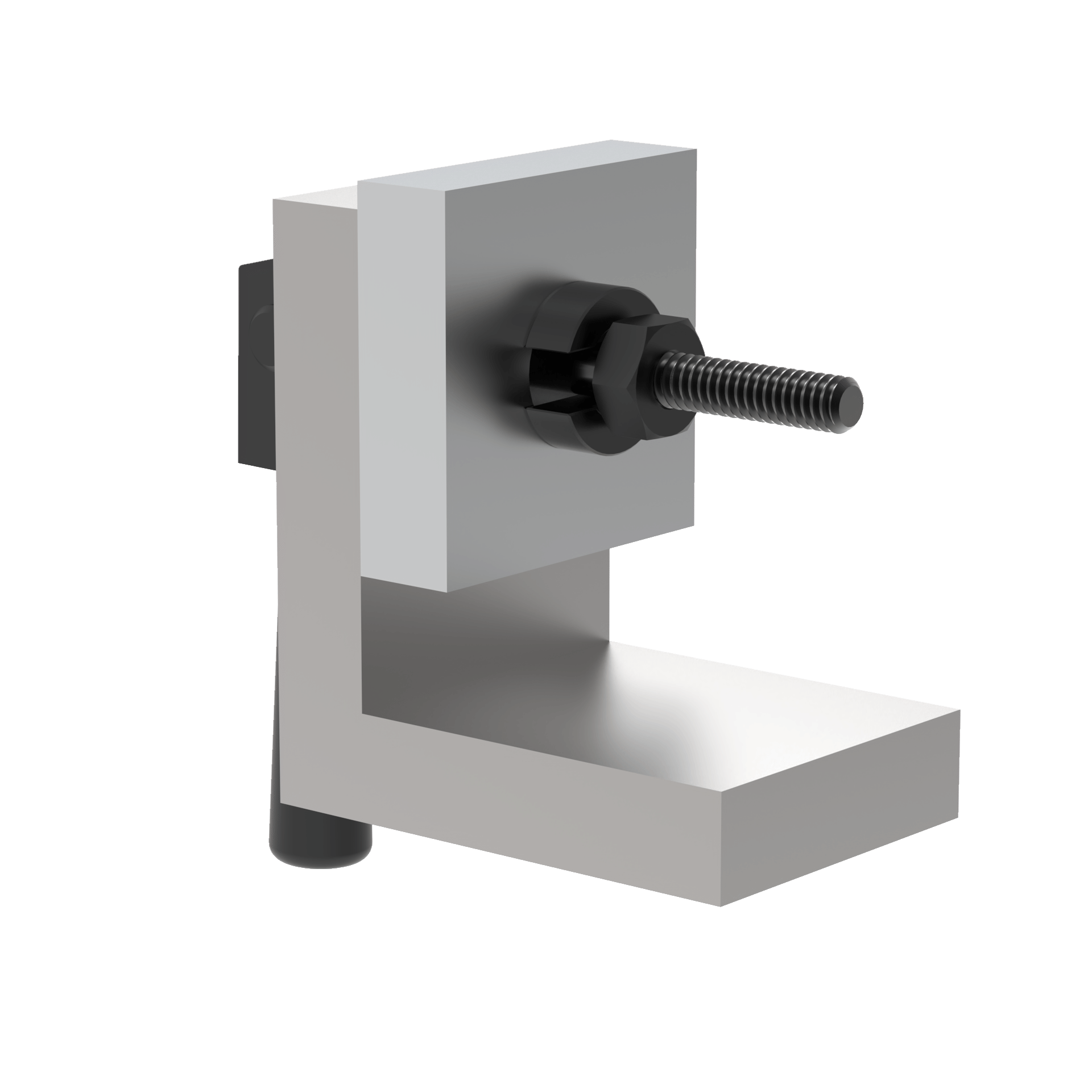
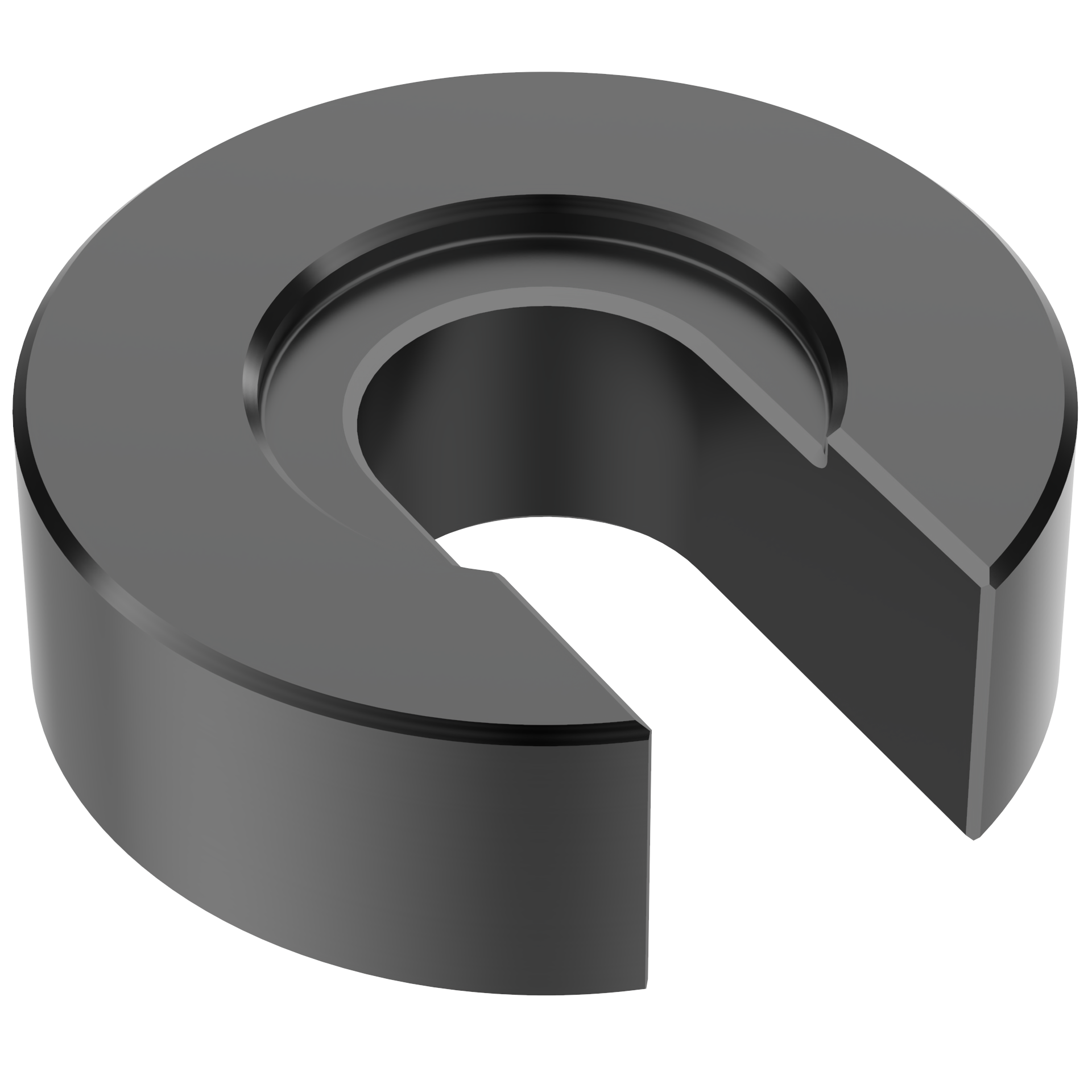
Quarter and Half-Turn screws operate generally as described. Like the C-Washer both of these fasteners are typically pre-inserted into a subplate. The fixture is then loaded over the fasteners. Unlike the C-Washer these fasteners are designed to be operated by hand without the need for tools. Without the need for tools, they are an excellent, captive, low-cost option for simple operations such as leak-testing and part marking where their lower retention force, due to their hand fastened nature, are not a disadvantage. They too must be located using means other than that of the fastener.
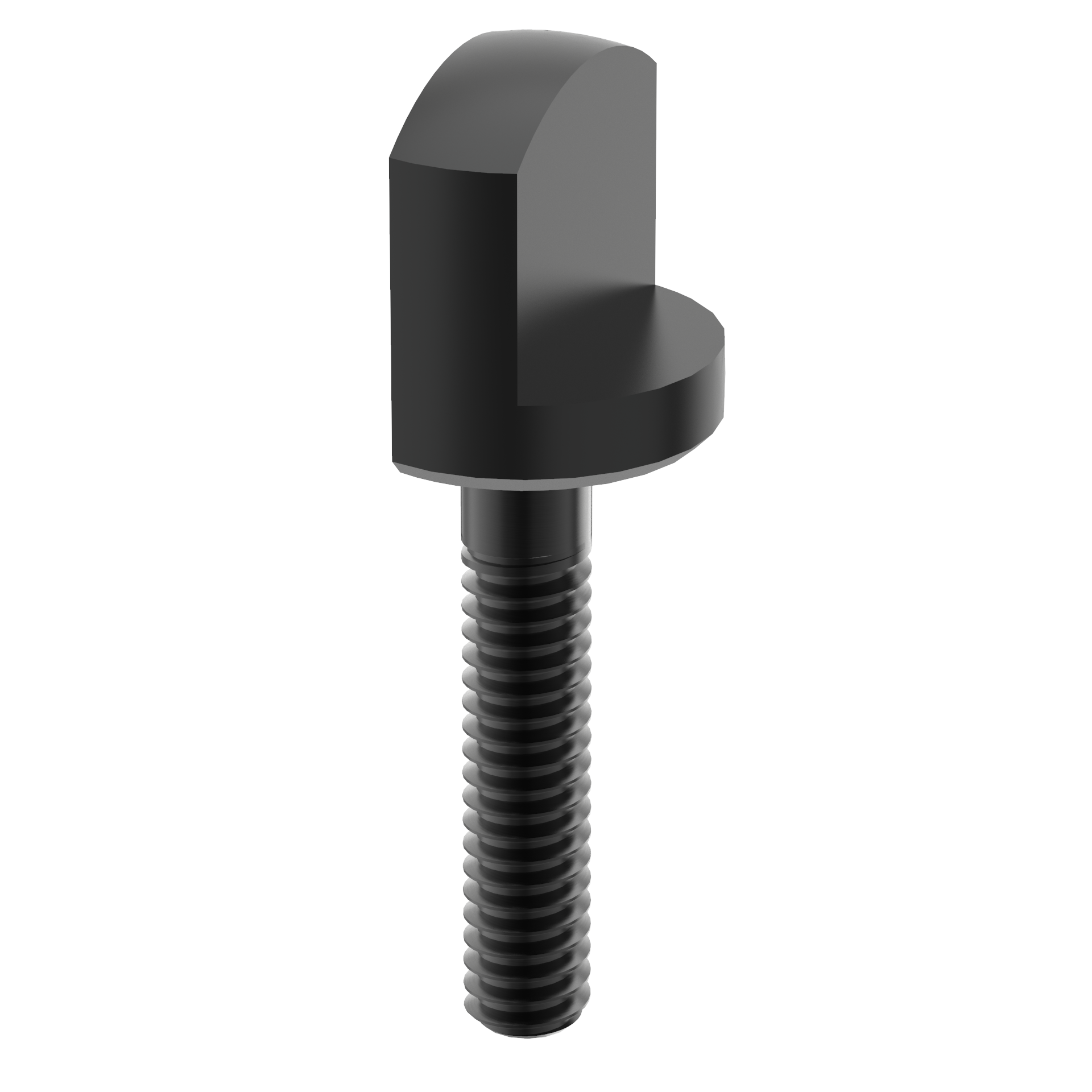