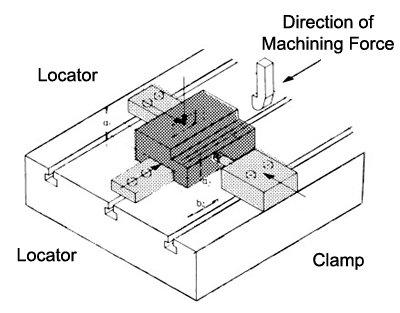
To increase the effectiveness and efficiency of a workholder, use locators to resist most machining forces, rather than relying only on clamping force. Using smaller, less-expensive clamps is usually possible if the workpiece is correctly located and the locators properly designed.
Locating the workpiece is the first basic function of a jig or fixture. Once located, the workpiece can be held in place by the clamps to prevent movement during the operational cycle.
Clamps serve two primary functions. First, they must hold the workpiece against its locators. Second, the clamps must prevent movement of the workpiece.
Clamps should not be used to resist the primary cutting forces. The only purpose of clamps is to maintain the position of the workpiece against the locators and resist the secondary cutting forces. The secondary cutting forces are those generated as the cutter leaves the workpiece.
In drilling, for example, the primary cutting forces are usually directed down and radially about the axis of the drill. The secondary forces are the forces that tend to lift the part as the drill breaks through the opposite side of the part. The clamps selected for an application need only be strong enough to hold the workpiece against the locators and resist the secondary cutting forces.
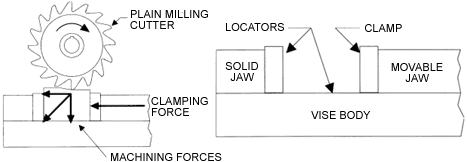
The relationship between the locators and clamps can be illustrated with a milling-machine vise. As shown above, the vise contains both locating and clamping elements. The solid jaw and vise body are the locators. The movable jaw is the clamp. The vise is normally positioned so that the locators resist the cutting forces. Directing the cutting forces into the solid jaw and vise body ensures the accuracy of the machining operation and prevents workpiece movement. In all workholders, it is important to direct the cutting forces into the locators. The movable vise jaw, like other clamps, simply holds the position of the workpiece against the locators.
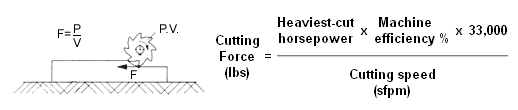
An important step in most fixture designs is looking at the planned machining operations to estimate cutting forces on the workpiece, both magnitude and direction. The "estimate" can be a rough guess based on experience, or a calculation based on machining data. One simple formula for force magnitude, shown above, is based on the physical relationship:
Please note: "heaviest-cut horsepower" is not total machine horsepower; rather it is the maximum horsepower actually used during the machining cycle. Typical machine efficiency is roughly 75% (.75). The number 33,000 is a units-conversion factor. The above formula only calculates force magnitude, not direction. Cutting force can have x-, y-, and/or z-axis components. Force direction (and magnitude) can vary drastically from the beginning, to the middle, to the end of the cut.
A typical machining-force calculation is shown above. Intuitively, force direction is virtually all horizontal in this example (negligible z-axis component). Direction varies between the x and y axes as the cut progresses.
The position of clamps on the workholder is just as important to the overall operation of the tool as the position of the locators. The selected clamps must hold the part against the locators without deforming the workpiece. Once again, since the purpose of locators is to resist all primary cutting forces generated in the operation, the clamps need only be large enough to hold the workpiece against the locators and to resist any secondary forces generated in the operation. To meet both these conditions, position the clamps at the most-rigid points of the workpiece.
With most workholders, this means positioning the clamps directly over the supporting elements in the baseplate of the workholder, shown at (a). In some cases the workpiece must be clamped against horizontal locators rather than the supports, shown at (b). In either case, the clamping force must be absorbed by the locating elements.
Evaluate workpiece-loading procedure and clamping sequence. Loading and clamping can be completely automatic, or involve some manual steps. To position the workpiece against locators, spring-loaded positioners (above) are often helpful. Sequence Valves are extremely useful to position hydraulically with push clamps before clamping. Total positioning force should be 30-50% of the workpiece's weight to overcome friction.
Decide how many parts you want to place on the fixture. For example, to place three workpieces on the above fixture, mini Swing Clamps are necessary. With only one workpiece, just about any clamp would do.