Strap clamps are one of the most common clamps used in woodworking, metalworking, and other manufacturing industries. They are simple in design and easy to use, making them a popular choice for securing workpieces.
The essential components of a strap clamp include a clamp strap, a fastening device, and heel support.
The clamping strap is the main component that wraps around the workpiece and holds it in place. The fastening device tightens the strap around the workpiece. It can be a variety of mechanisms, such as a screw, lever, or ratchet. The heel support is part of the clamp that provides stability and support to the clamp strap.
One of the benefits of strap clamps is their versatility. These devices secure a variety of workpieces, from small and simple to large and complex. Strap clamps, sometimes known as band clamps, can also be used with other clamps, such as bar or pipe clamps, to provide additional support.
This comprehensive guide will delve into the different types of strap clamps available and how they work. Whether you’re a beginner or an experienced woodworker, understanding the ins and outs of strap clamps is essential for successful clamping and a satisfying project outcome.
How Does A Strap Clamp Work?
All clamp straps work on the mechanical principle of the lever. The three basic styles of strap clamps are described by lever arrangements, called first, second, and third-class levers. The classes do not represent importance or preference levels; instead, they show distinctions in the mechanical actions of each lever style.
The clamping force on the workpiece depends on the relative position of the workpiece, fastening element, and fulcrum. All strap clamps are essentially beams loaded in bending.
For most calculations, this force is known. The clamping force is the actual force applied to the workpiece during the clamping operation, a fractional portion of the applied force. The reaction force is the force generated on the fulcrum. Changing the positions of the various elements affects the amount of clamping force.
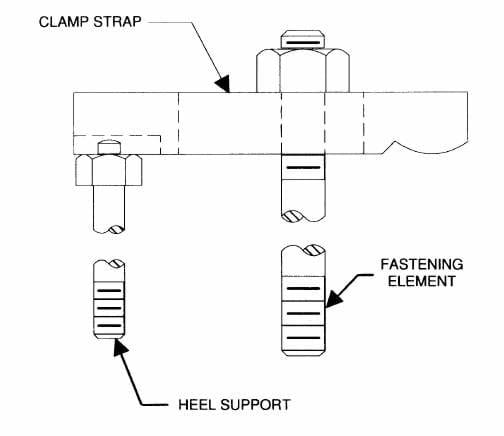
Types of Clamp Straps
Clamp straps come in a variety of forms. Selecting the correct clamp strap for a task is essential to a workholder’s operation and efficiency. Clamp straps vary in both material and basic shape or style. The most common material for clamp straps is carburized-hardened carbon steel, but forged steel, stainless steel, and aluminum clamp straps are also available.
Below are some of the common types of clamp straps available from Carr Lane Mfg.
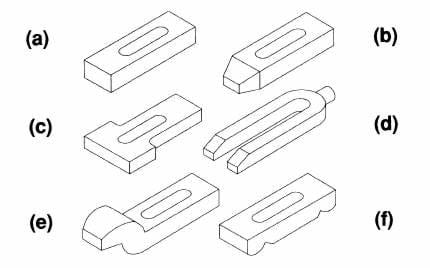
Slotted-Heel Clamp Straps
The slotted-heel clamp strap has a slotted heel to locate the clamp strap on the clamp rest. This slotted heel, combined with the stud hole, allows the clamp strap to move completely clear of the workpiece for part removal and reloading.
You can find these clamps in many lengths and stud sizes in either carbon or stainless steel. The contact area of these clamp straps is available in radius-nose, plain-nose, and padded-nose styles. Slotted-heel clamp straps are also available in a gooseneck version.
Explore Slotted Heel Clamp Straps
Tapped-Heel Clamp Straps
The tapped-heel clamp strap has a tapped hole in the heel end. The component installed in this hole can be either a screw clamp that applies clamping force or an adjustable heel rest. When used to mount an adjustable heel rest, the complete clamp is a third-class-lever arrangement, but when used to mount a screw clamp, it employs a first-class-lever action.
Like slotted-heel clamp straps, tapped-heel straps come in many sizes of either carbon or stainless steel. The contact area of these clamp straps is also available in radius-nose or padded-nose styles.
Explore Taped-Heel Clamp Straps
Double-End Clamp Straps
The double-end clamp strap holds workpieces on both ends. This clamp strap has a radius nose on both ends.
This design provides equal clamping force on both ends, even if height variations exist in the workpieces. Double-end clamp straps are also available in a gooseneck version.
Explore Double-End Clamp Straps
Step Clamps
Step clamps are one of the more common clamp strap designs. These clamp straps have a series of serrations, or steps, machined in their heel.
These steps engage similar steps in a matching heel block. This design allows adjustable positioning for different workpiece heights.
Explore Step Clamps
Forged U Clamps
The forged U clamp is a general-purpose clamp strap. Both the U end and pin end of the forged steel clamp strap can clamp a workpiece.
The U end permits strap removal when unclamped. The pin end is often used with limited space or for clamping in horizontal holes.
Explore Forged U Clamps
Forged Adjustable Clamps
Forged adjustable clamps are well-suited where heel support could interfere with the setup. These clamps are made as a complete unit and can accommodate a variety of workpiece heights.
The steel pivot allows the fastening element to clamp at all elevations securely.
This clamp is available in either forged steel or aluminum alloy.
Explore Forged Adjustable Clamps
Studs and Bolts
Two primary threaded fasteners used for strap clamps are studs and bolts. Studs are the most common fastener for strap clamps. One end of the stud mounts in a T nut; the other applies the holding force with a nut.
Washers are standard in many workholding applications and for use with strap clamps. These include flat washers, C washers, swing C washers, knurled-face washers, and spherical washers.
Explore Studs and Bolts
Fastening Elements
The fastening element of a clamp strap is the device that applies force to the clamp. The two general fastening elements for strap clamps are threaded fasteners and cam handles. Threaded fasteners include bolts, studs, washers, nuts, and knobs.
Explore Fastening Elements
Cam Handles
Cam handles act as the fastening element with strap clamps. Double-cam handles use an eyebolt arrangement, which uses a clevis pin as the primary mount for the double-cam handle.
The benefit of cam-action clamps is the speed of operation. However, one word of caution: cam clamps rely on the friction between the cam lobe and the clamp or workpiece to maintain clamping force. Some operations with excessive vibration could cause a cam clamp to loosen due to the inertial force of the handle.
Explore Cam Handles
Nuts and Knobs
The nuts and knobs for strap assemblies come in a variety of styles. They include the T nut, flange nut, spherical nut-and-washer set, hex nut, jam nut, knurled check nut, knurled nut, acorn nut, and coupling nut.
In addition to the nuts, knobs are also used with straps. They include the palm-grip knob, the hand knob, and the bar knob.
Explore Nuts | Explore Knobs
Heel Supports
The heel supports for straps provide support at the end opposite the clamping point. The two basic types are threaded and block supports.
Depending on the tool’s design, threaded supports are mounted either in the strap or the workholder base. Block supports can be custom-made to suit the clamp height, or you can use standard step blocks.
Common heel supports for strap clamps include clamp rests, clamp rest screws, and stud leveling feet.
Explore Clamp Rests
Other Clamp Strap Accessories
Other accessories for clamp straps include guide blocks, clamp springs, and finger pins. Guide blocks work as a rear slide block for tapped-heel-type clamp straps. These blocks position the clamping screw and reduce wear on the tool body.
Clamp springs are placed over the stud, between the clamp strap and the tool body. This spring makes loading and unloading the workholder easier because it keeps the clamp strap elevated off the workpiece. Finger pins are occasionally installed in clamp straps to aid sliding movement. Depending on the setup, finger pins can be used on either one or both sides of the clamp strap.
Choosing the Right Strap Clamp for Your Project
While the specific types of clamps and their applications may vary depending on the industry, the general principles of selecting the suitable clamp for your project are relatively universal.
For example, in metalworking, you may need to consider factors such as the material clamped, the size and shape of the workpiece, and the level of clamping force required. In automotive repair, you may need to select clamps capable of securely holding different components in place during maintenance or repair procedures.
Consider the size of the project. Strap clamps come in various lengths and widths, so choosing one appropriate for your workpiece’s size is essential. If you are working on a larger project, you may need a longer strap clamp to secure all the pieces tightly.
Strap Clamp Safety Considerations
It’s important to keep safety in mind when using a strap clamp. The tension applied by a strap clamp can be significant, so you should always wear eye protection and gloves when tightening the clamp.
Be careful not to overtighten the clamp, as this can damage the workpiece or cause the clamp to fail. Ensure the clamp is securely attached to a stable work surface or workbench. When working with large or heavy objects, it’s important to have help from a partner to ensure that the workpiece is safely and securely held in place.
Explore Strap Clamps At Carr Lane Mfg.
If you’re looking for high-quality strap clamps for your next project, look no further than Carr Lane Mfg. Our selection of strap clamps includes a variety of sizes and styles to fit your specific needs.
Browse our selection of strap clamps today and see the difference for yourself!
In-Stock Clamp Straps