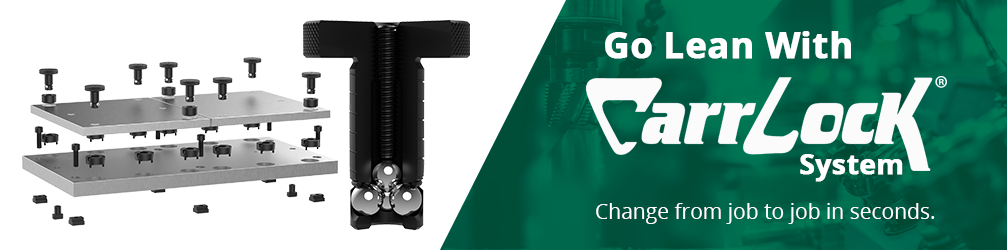
In North America the predominant type of Quick-Change system is the Carr Lock Mounting System®. This mechanical system provides high accuracy locating, typically +/-0.0005”, and good retention force. The Carr Lock System consists of three components, the Carr Lock Clamp, Liner Bushing, and Receiver Bushing.
The clamps have precision ground shanks available in sizes 13mm, 16mm, 20mm, 25mm, 30mm, 35mm, and 50mm. They come in lengths for standard plate thicknesses, (two lengths for each diameter) in either metric lengths from 13mm to 25mm for metric plates, or 0.50” to 2.00” for inch dimension plates. Carr Lock® Clamps are actuated by turning the clamping screw with a hex wrench, which advances the large center ball, pushing the three clamping balls outward. These balls engage the angled ID section of the Receiver Bushing, pulling the clamp firmly downward. See Figure 5-2. Clamps with 16mm and 20mm shank diameter are optionally available with a Knurled Head Screw for quick, tool-less actuation.
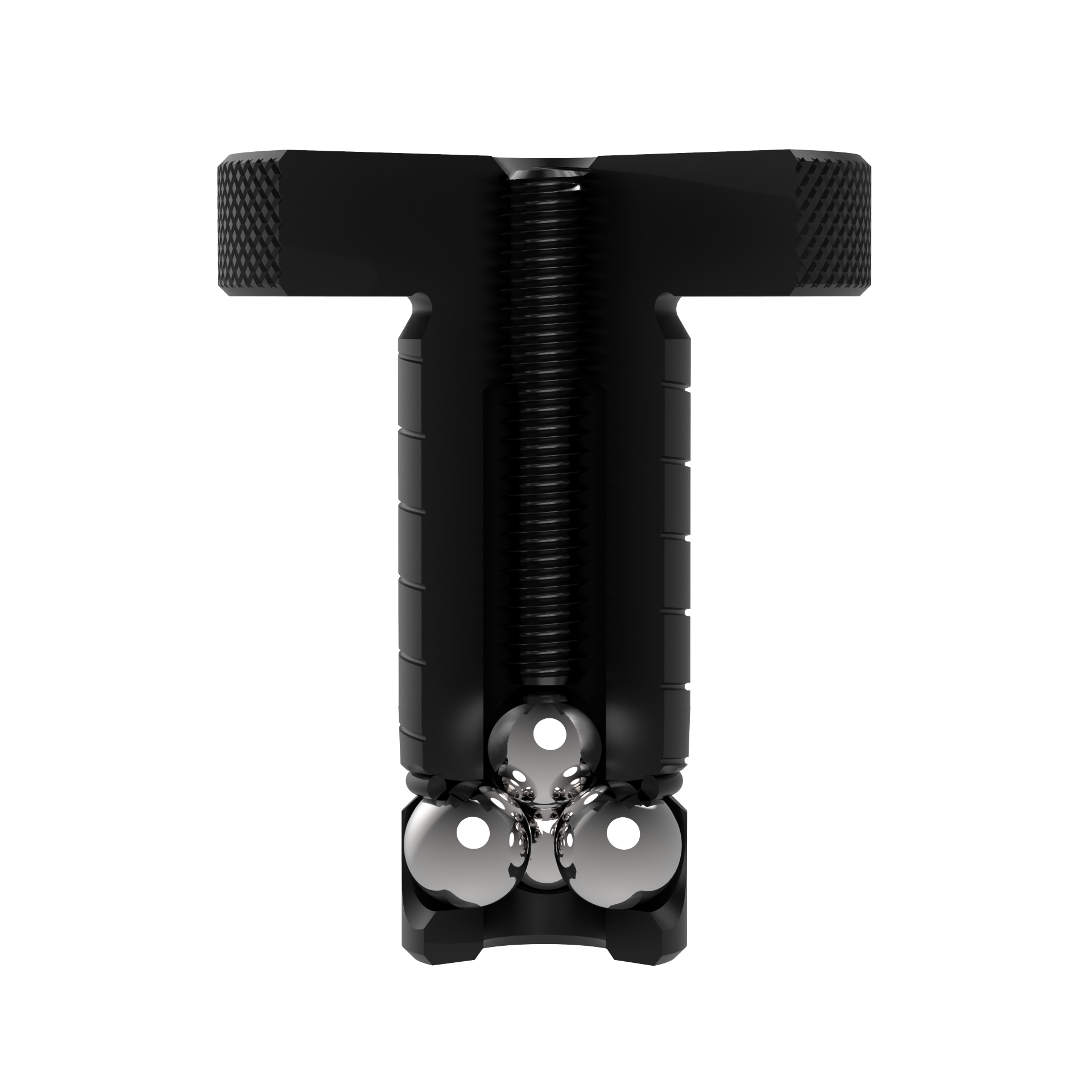
Headless Carr Lock Clamps functional identically to headed clamps with a significantly reduced space requirement on the tool. Additionally, the headless clamp can be installed entirely below the top surface of the tool with only a hole in the tool for the activation of the clamp. (with an Allen wrench) To provide for the lowest overall size the headless version does not use liner bushings. Instead it uses two variants, primary and secondary. The primary clamp is used to accurately locate your plate while the looser fit on the secondary clamp reduces binding. Because the connection to the tool is made with threads, and due to thread tolerances the accuracy of this system is a bit reduced from the headed version. Accuracy can be improved by using multiple secondary clamps and a round and diamond pin.
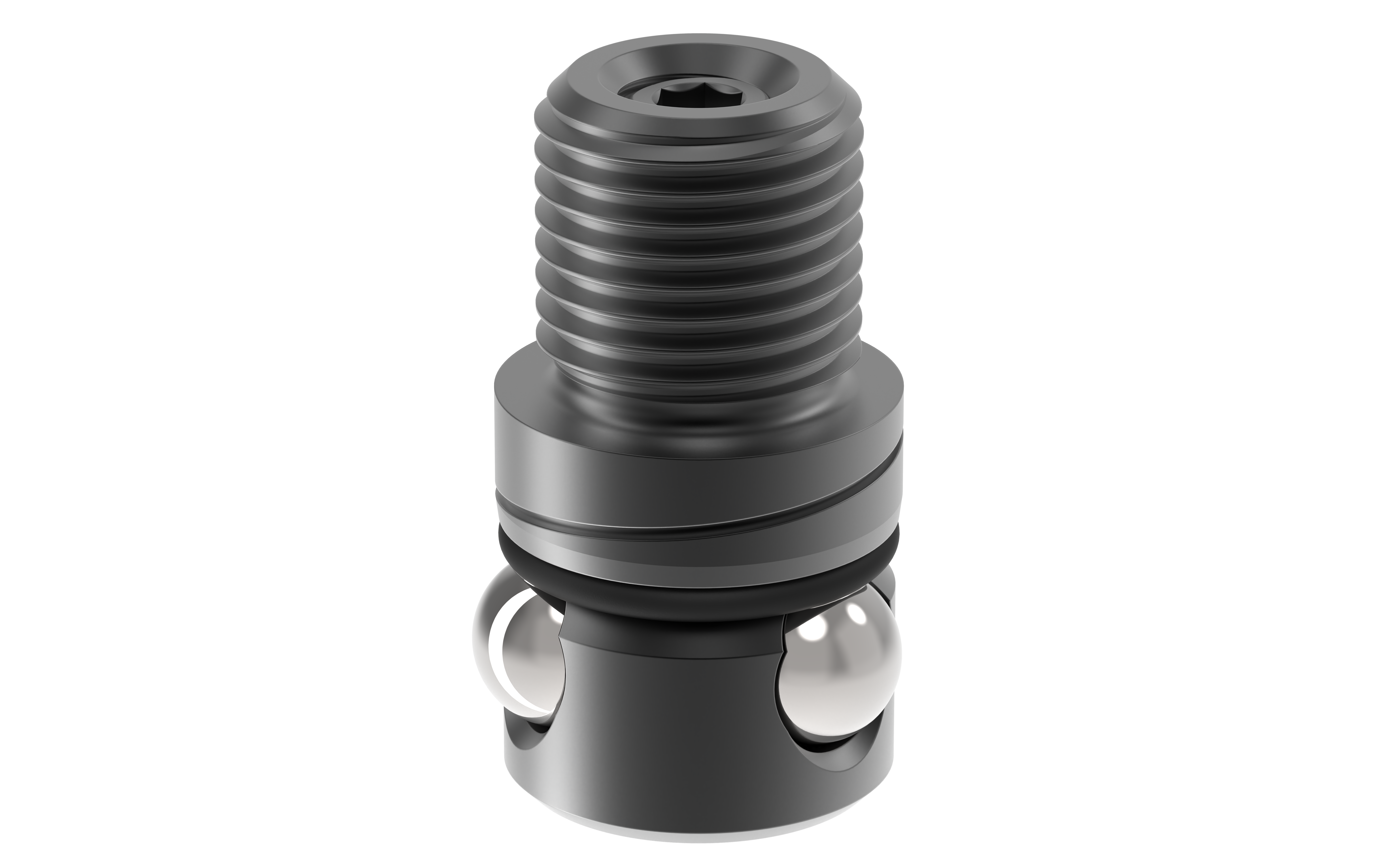
The Carr Lock® System requires that each fixture plate have one mounting hole designated as the primary reference hole (Primary Liner Bushing) and one mounting hole designated as the secondary reference hole (Secondary Liner Bushing or Slotted Locator Bushing). All other mounting holes should be drilled clearance holes not locating, .015-.030" over nominal size used for clamping only. Secondary Liners have slight ID clearance (+.0010/+.0020" tolerance) to avoid binding. Slotted Locator Bushings have a tight ID tolerance in one direction and full relief in the perpendicular direction. Slotted Locator Bushings provide better accuracy than Secondary Liners, but take a few extra steps to install, and are not available in all sizes.
The accuracy and the holding force of the Carr Lock® System require the clamps be used with the appropriate receiver bushings. Receiver bushings come in two styles, face mount or back mount. The face mount bushings are a slip fit into a precision bored hole and are held in place with three Socket Head Cap Screws, while the back mount bushings are a light press fit installed from the bottom of the fixture plate. With either bushing type, the installation holes must be jig bored for accurate size and location. Installed bushings will be approximately .012" below the subplate’s top surface.
Due to the highly efficient design of the clamps, the torque required to clamp them is fairly low – one foot pound of torque on the 13 mm diameter clamp delivers 750 pounds of hold down force. On the largest size, 50 mm, 38 foot pounds of torque will result in 20,000 pounds of hold down force. Given the low amounts of torque required, preset torque wrenches are available to prevent the application of excess torque, which can break the clamps. These wrenches, with attached hex driver, are available for the 13, 16, 20 and 25 mm diameter clamps.
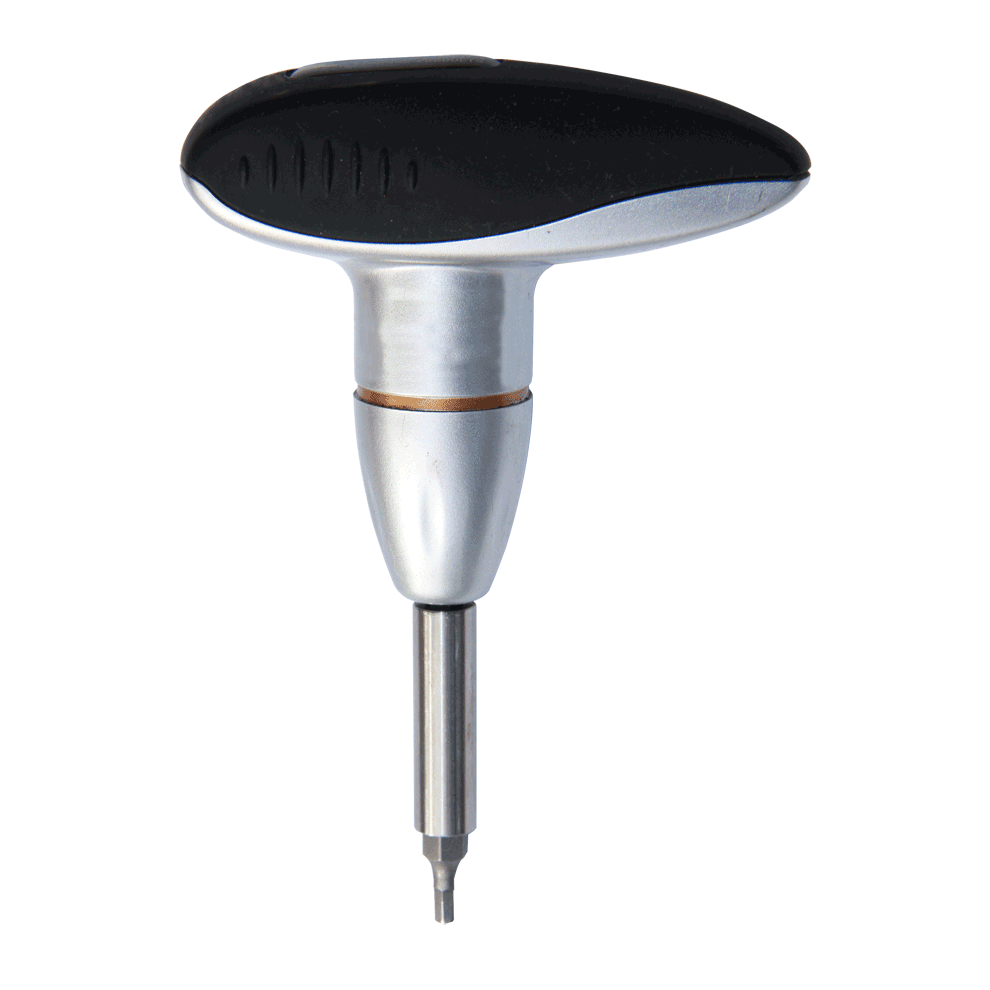
For reasons of simplicity, pre-assembled kits are available for many machines, from table sizes of 12” X 14” to 500mm X 1000mm (20” X 40”). These kits include not just the subplate, fixture plate(s), and the appropriate number of clamps, but also all items needed to mount the subplate on the machine, T Nuts, Socket Head Cap Screws, and Sure-Lock™ Fixture Keys. Two locating holes for Sure-Lock™ Fixture Keys are provided for alignment with a slotted machine table. Fasten to the machine using the four, six, or eight mounting slots provided, with Socket Head Cap Screws and T Nuts to match the machine table.
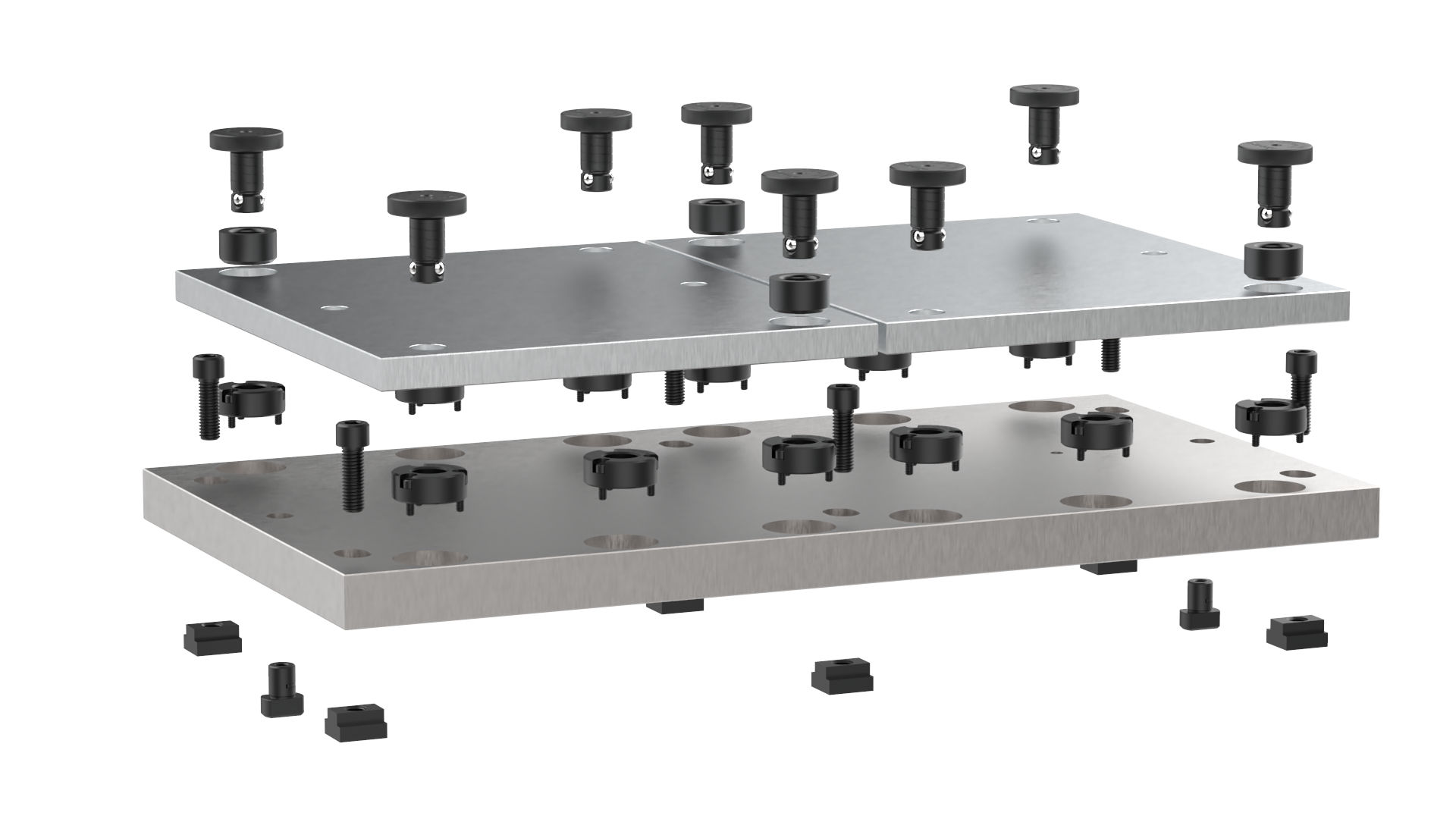
The subplate is essentially permanently attached to the machine table. Once it is properly located and fastened, it is ready for the mounting of the fixture plates. Each subplate is made from A-36 precision ground plate, and contains a series of highly accurate receiver bushings to allow the mounting of different sizes and styles of fixture plates. These plates, and their associated kits are readily available for many popular machine table sizes, from 12” X 14” up to 500 mm X 1000 mm (20 in. X 40 in.). Different subplates have varied sizes and arrangements of receiver bushings allowing the installation of different fixture plates, including multiples, up to four vise plates on the largest subplates. Using multiple fixture plates, or vises, allows the machining of two or more different parts in the same machine cycle.
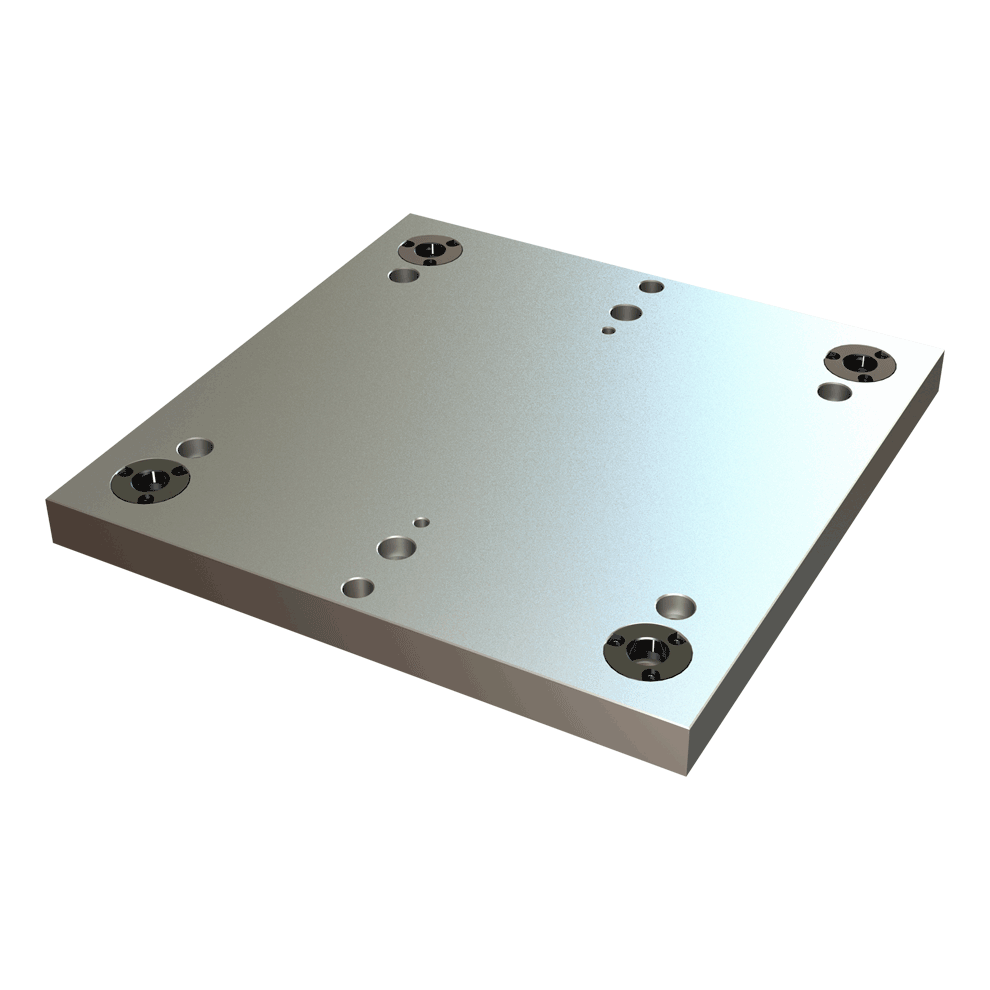
Made from MIC-6 aluminum, fixture plates are available to fit any of the various subplates, from 12” X 14” to 500mm X 1000mm (20” X 40”). Each plate has two bushed holes, one a primary liner, and the other a secondary liner. The other two holes in the plate are clearance holes which are used for clamping, but not location. Carr Lock® Fixture Plates also have two fixture-key holes for conventional mounting directly on a slotted machine table using Sure-Lock™ Fixture Keys. Vise fixture plates for mounting vises are also available in a design that allows the maximum utilization of the machine by mounting up to four vises on one subplate.
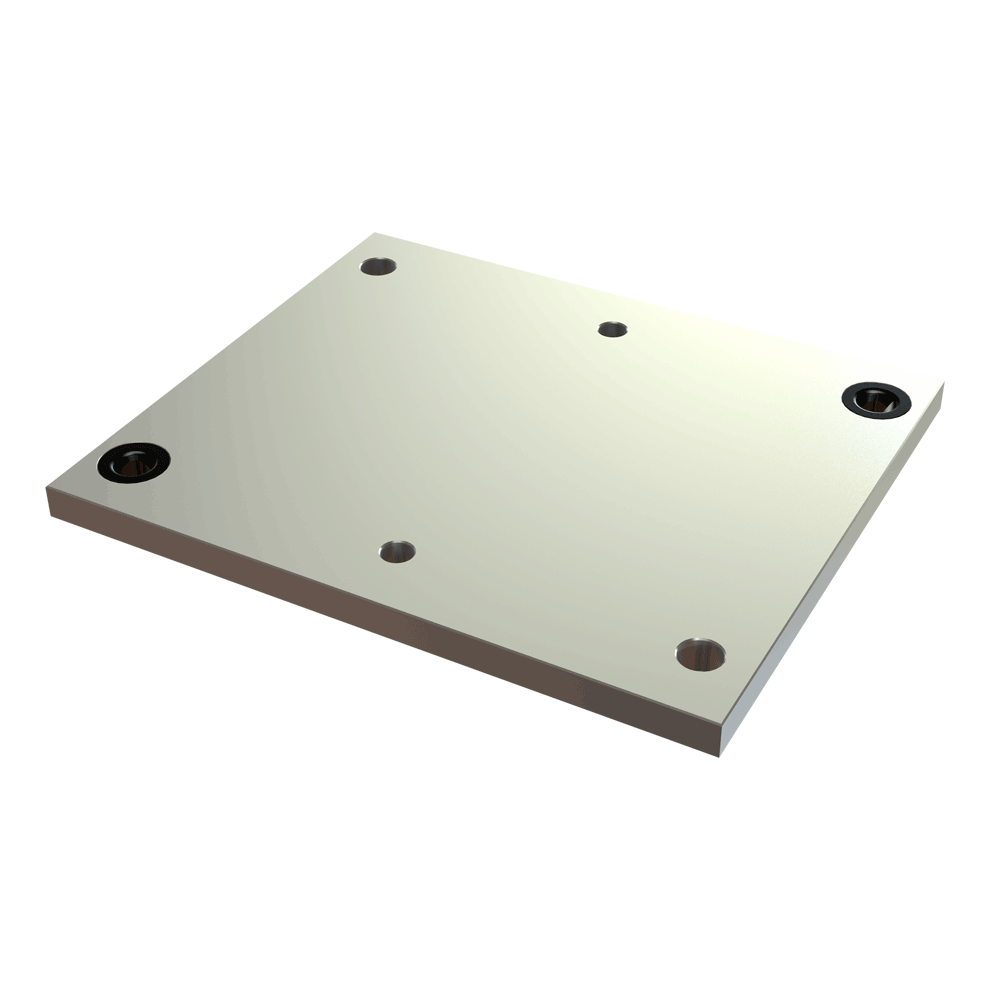
Given the high precision inherent in the Carr Lock® System, it is often ideal to machine the fixture plate on the machine on which it will be run, or, at least, another precision machine with a Carr Lock® subplate installed. A consideration to keep in mind in these cases is avoiding damage to the subplate, which can be caused by drilling or milling through the fixture plate. An easy way to avoid this is through the use of a Carr Lock® Machining Kit. The kit consists of four extra-long Carr Lock® Clamps, used together with four precision-height spacers, providing ample clearance underneath the fixture plate to allow through-hole machining without damaging the subplate. The kit also includes an extra four spacers to use as additional supports under large plates.
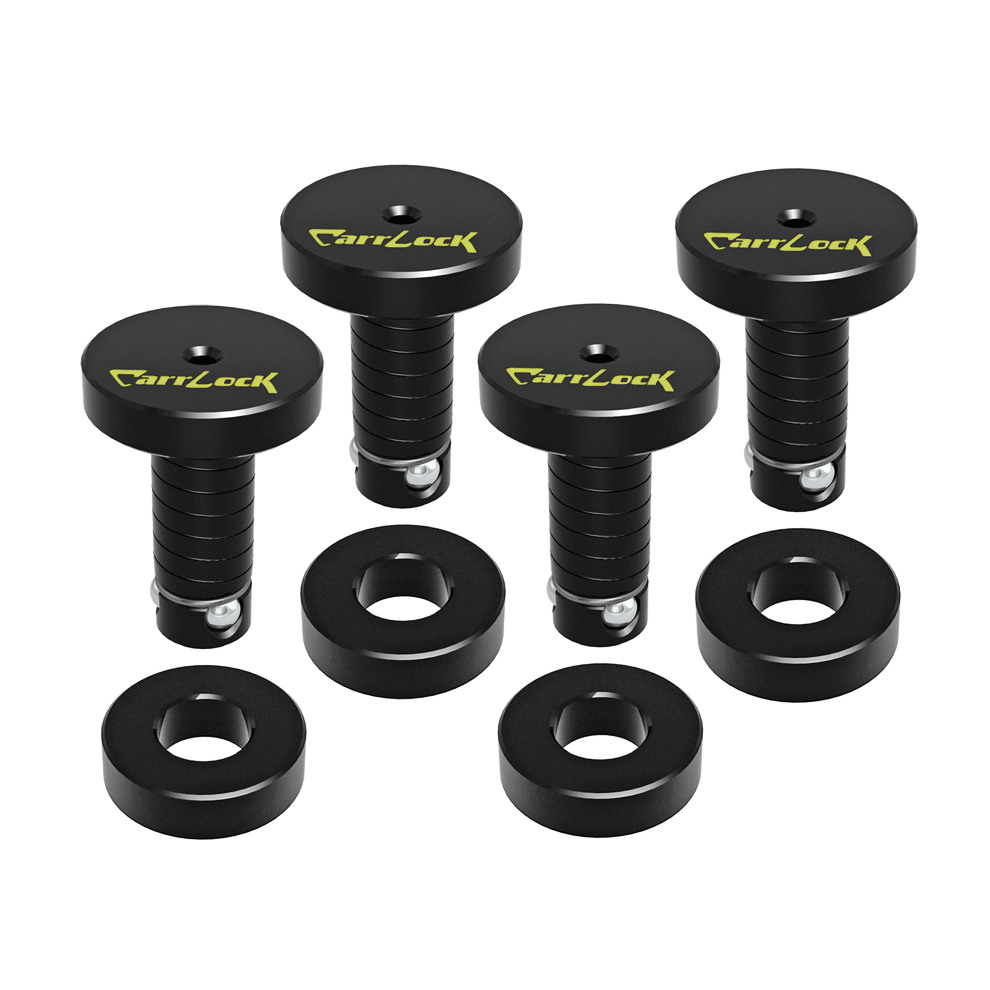
One concern that may arise when using a fixture plate or plates on a larger subplate is the propensity of chips to collect in unoccupied receiver bushings. An easy solution to this condition is the use of Carr Lock® plugs. These plugs are designed to close off the hole, and prevent chips from packing into bushings and necessitating lots of work to clean them out so they may be used for the next setup, thus negating much of the “quick change” aspect of the system. These inexpensive plastic plugs are easy to install and remove since they are a light press fit in the bushing. They are available for all sizes of receiver bushings.
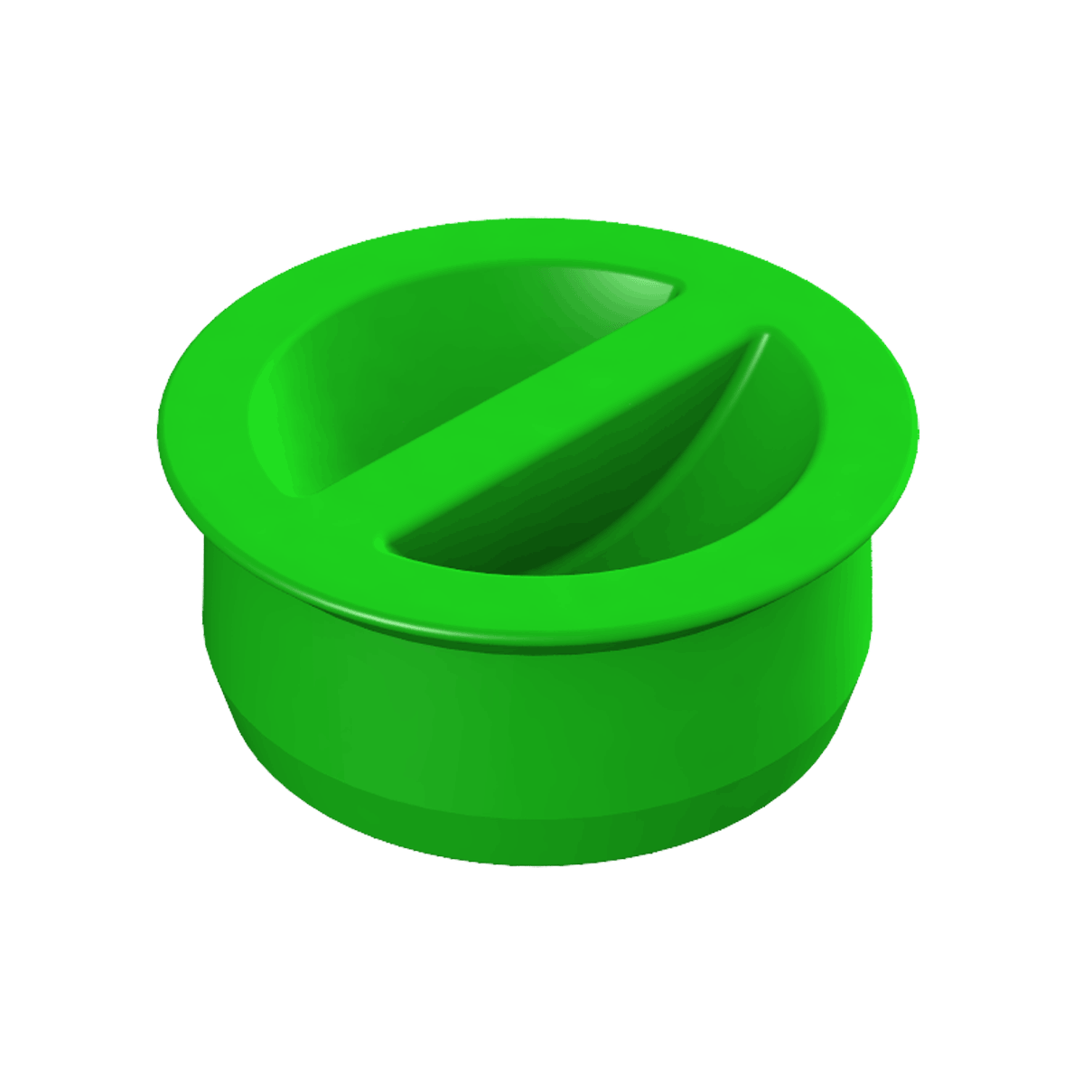